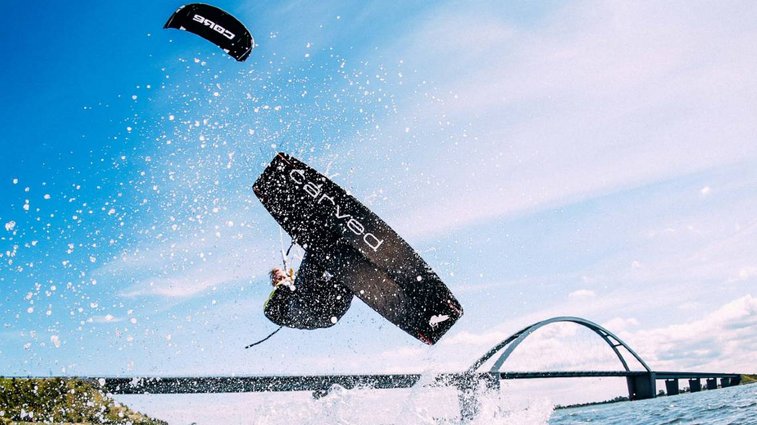
Kitesurfing requires not only athletic ability but also durable equipment.
© CORE Kiteboarding GmbH
On the Baltic Sea island of Fehmarn, one of the world's leading kiteboard manufacturers produces durable boards for the whole world. CORE Kiteboarding GmbH uses a special laminating process to produce boards that can hold up to the hard impact from repeatedly hitting the water. With the help of vacuum technology from VACUUBRAND, the production process eliminates air bubbles which would reduce the strength of the kiteboard.
The exhilaration of feeling the wind as athletes take flight over the water while kitesurfing inspires athletes worldwide. The combination of surfboard and kite makes this extreme sport so special – and requires not only athleticism but also reliable equipment. This is because the material is subjected to heavy loads from the forces of nature and the surfer's jumps.
One hotspot for water sports enthusiasts is the Baltic Sea island of Fehmarn. It is here that CORE Kiteboarding GmbH began to make especially high-quality boards in 2001. It is no coincidence that the entire team consists of passionate kitesurfers. This means that quality is close to their hearts and they know exactly what is required of their equipment. Today CORE Kiteboarding is one of the leading kiteboard manufacturers, selling their boards to customers all over the world. Every board in the "Carved Custom" product line, for example, is individually manufactured and unique. Thanks to an elaborate, manual lamination process, it offers superior material bonding. This is important, for example, when athletes jump and place a great amount of stress on the board, where the board must not break.
Laminating with the vacuum infusion process
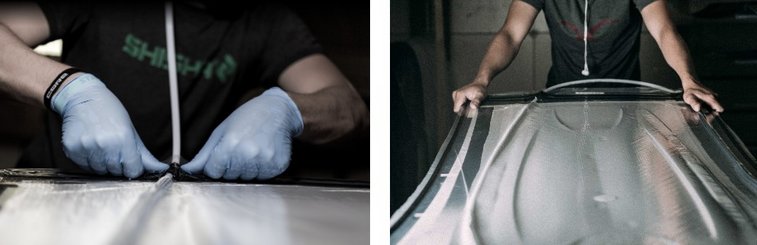
Lamination of the wooden body in an evacuated foil pouch
© CORE Kiteboarding GmbH
The lamination process of the “Carved Custom” kiteboards is similar to other surface technology applications, e.g. boat and aircraft construction or wind turbines, using a multi-component resin. A high-performance carbon fiber jacket with an optimized scrim structure serves as fiber reinforcement. The ratio of these two composites – resin and fibers – is optimized by a special vacuum infusion process. Each “Carved Custom” kiteboard requires significantly less resin and offers a higher fiber volume ratio than conventional carbon fiber technologies. The advantages are noticeable on the water:
Thanks to our special vacuum infusion process, significantly less weight and noticeably crisper performance is possible with the Carved Custom boards.
How does vacuum technology support the entire production process?
- Venting of resin and hardener: Vacuum is applied prior to the mixing process of the multi-component resin. A vacuum pump ensures that air inclusions, which would otherwise endanger the stability of the material, are eliminated from the two components. The two components can then be combined in a resin mixing machine. This is done just before the actual laminating process to prevent the resin and hardener from reacting and curing prematurely.
- Evacuation of wood core and mold: Vacuum also supports the preparation of the actual core of the kite board. For this purpose, the wood core is located in the middle of a mold, where the carbon fiber fabric is applied on the top and bottom for an optimal laminate structure. Then a foil is applied over the edge of the mold as a seal. A vacuum pump then creates negative pressure, which creates a physical force that removes trapped air from the wood core and evacuates the mold.
- Resin impregnation: In the subsequent vacuum infusion process, a vacuum pump distributes the liquid resin mixture evenly between the mold and the foil. The vacuum also causes the wood core to be pressed into the mold and the carbon fibers to be properly aligned on it. The subsequent resin curing process also takes place under constant vacuum and lasts several hours. A collection container in front of the vacuum pump - a so-called resin trap - prevents resin from reaching the pump and blocking it.
Low maintenance vacuum pumps for production process
CORE Kiteboarding has been using chemistry diaphragm pumps in the production of high quality kiteboards for many years. An oil-sealed rotary vane pump was initially selected, but this pump technology turned out to be unsuitable because it was affected by rust after a short time. After intensive consultation with VACUUBRAND application specialists and testing of an oil-free diaphragm pump, it soon became clear that the chemically resistant MD 4C diaphragm pump provided the necessary resistance to condensate formation inside the pump and provided more than enough vacuum to meet the required process vacuum of 3-4 mbar.
The MD 4C vacuum pump has sufficient pumping speed to degas four boards simultaneously and still achieve the required vacuum level. It enables the continuous pumping of corrosive gases throughout the entire curing process. The robust and durable design of the vacuum pump enables continuous operation day and night, maximizing production capacity during the peak summer season, for example.
Chemistry diaphragm pumps as corrosion-resistant solution
During the coating process, the pressure drops below 25 mbar. This removes the air bubbles from the resin while simultaneously evaporating water content in the resin. In the vacuum pump, the gas condenses and becomes liquid again, producing low-ion, corrosive water.
An oil-free chemistry diaphragm pump offers the advantage that the wetted parts of the pump consist entirely of fluoroplastics that are optimally resistant to chemicals. Even when pumping aggressive media there is no risk of corrosion and the performance of the pump is maintained.
In an oil-sealed rotary vane pump, the low-ion water accumulates in the oil and attacks metals in the pump - corrosion occurs. The performance of the pump decreases until it can fail completely.
Kompetenter Partner für perfekte Boards
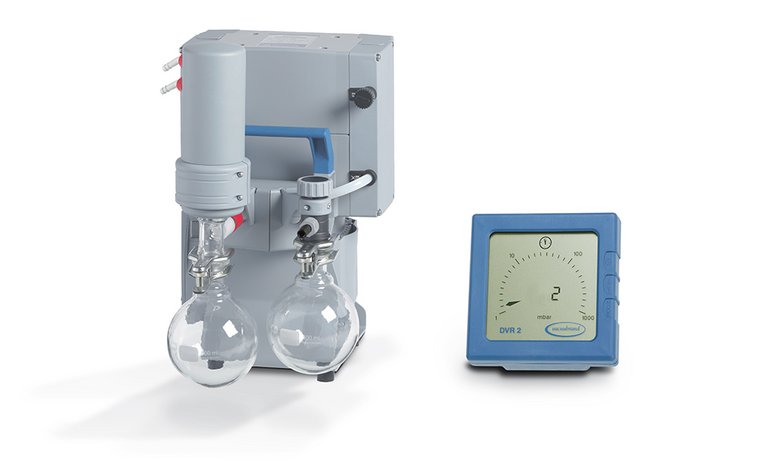
Durable products for vacuum supply and measurement from VACUUBRAND
Bei CORE Kiteboarding kommen gleich zwei der chemiebeständigen Membranpumpen MD 4C zum Einsatz. Zur Überprüfung des Vakuumniveaus verwendet das Unternehmen das vollelektronische Messgerät DVR2 von VACUUBRAND. Dank der einfachen Bedienung und der kombinierten digitalen/analogen Druckanzeige lassen sich Messwerte schnell und präzise erfassen. Die Vakuumversorgung mit Produkten von VACUUBRAND stellt seit 2009 eine wartungsarme und verlässliche Lösung für das Produktionsverfahren von CORE Kiteboarding dar.
VACUUBRAND's oil-free chemistry diaphragm pumps are an optimal alternative to corrosion-prone rotary vane pumps. They contribute significantly to the success of our efficient vacuum infusion process